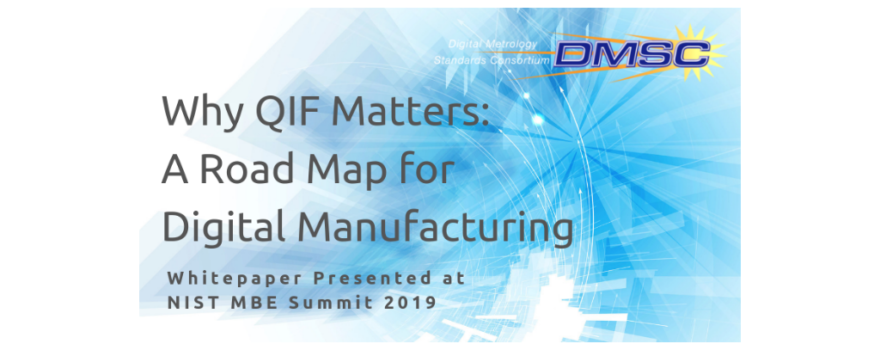
This paper was presented at the NIST MBE Summit in April 2019. It discusses how the ANSI DMSC Quality Information Framework (QIF) standard provides benefit to the Model-Based Enterprise (MBE) in two important ways: (1) automation of cyber-physical processes, allowing faster realization of higher quality products at lower cost, and (2) by providing traceability of massive quantities of measurement-related data to the authority product definition model. Over the last decade, efforts have been made to develop digital interoperability standards that address the connection points for information transfer through the product lifecycle. Through early work in the Automotive Industry Action Group (AIAG) and the Digital Metrology Standards Consortium (DMSC), new data models have emerged and achieved significant maturity levels.
The benefits of automation and business process systemization are made possible with meaningful, semantic data packaged in the QIF format. With Model Based Definition (MBD) data (i.e., PMI, FT&A, etc.) becoming more commonplace, QIF is becoming an attractive complete and unambiguous MBD delivery mechanism for industrial end users. In addition to automation benefits, QIF helps to provide data traceability in this age of Big Data, where traceability is sorely needed. MBE provides a paradigm for organizing this data by mapping it all to a meaningful product definition: the master model-based definition enabled by a product data management system. QIF is designed to instantiate this MBE approach to data management.
This paper was authored by a team of DMSC Board Members and will explain the background for why QIF is needed, and the features built into QIF which will ensure that it is equipped to handle the needs of modern industry.
BACKGROUND
Today’s manufacturing enterprise is plagued with the problem of disconnected, disorganized, and duplicated data. Furthermore, recent advances have seen an exponential increase in the volume of industrial data being generated, particularly data related to computer-controlled systems of all types. Terms like “Industrial Internet of Things” (IIoT) and “Industry 4.0” describe this revolution in big data. However, fundamental issues exist that need resolution. First, the majority of data is only minimally accessible and is unable to be mapped to data from other domains of a manufacturing enterprise. For example, how does raw data collected from a sensor embedded in a jet engine gets mapped to the machine tool operation which machined the blades or the shaft of the engine? A mapping of this type would require a human-in-the-loop to carry out the association based on a tedious study of the part serial number, then a review of the records for the manufacturing process, then the machine tool reporting logs, and finally then a hand-generated mapping to the machining of the feature in question. Reliance on a human-in-the-loop presents the following issues: it is a tedious process of high cognitive load which introduces errors, it is costly, it is not an efficient use of engineer’s time, and it prevents software algorithms for automatically mining the data for meaningful patterns and anomalies. A second fundamental problem faced in the field of industrial big data is the inaccessibility of the different data formats encountered. Data is stored in a variety of file formats (e.g., PDF, TXT, TIF, CSV, XLS, STEP, JT, IGES, PRT, QIF, XML, etc.). Some of these formats are proprietary, and require costly software tools to access the data. Other formats are common for archival, but are of minimal utility for software data mining (e.g., a coordinate measuring machine (CMM) inspection report stored in PDF format). Therefore, the issue of non-robust data formats prevents industry from easily connecting troves of data to the digital thread.
THE QUALITY INFORMATION FRAMEWORK (QIF)
The Quality Information Framework (QIF) was created by a group of manufacturers, software and hardware vendors, and metrology experts within the Digital Metrology Standards Consortium (DMSC) as a response to this dilemma. QIF is a feature-based ontology of manufacturing metadata, built on XML technology, with the foundational requirement of maintaining traceability of all metadata to the “single source of truth” – the product and all its components as defined in CAD/MBD. It is an open, ANSI standard which includes support for a complete semantic derivative Model Based Definition (MBD) model, measurement planning information, and measurement results information. This characterization allows users to establish a Digital Twin by capturing the duality of aspects of manufacturing data: the as-designed product, and the as-manufactured product – including the mappings between the two aspects …
Click here to read the complete whitepaper.