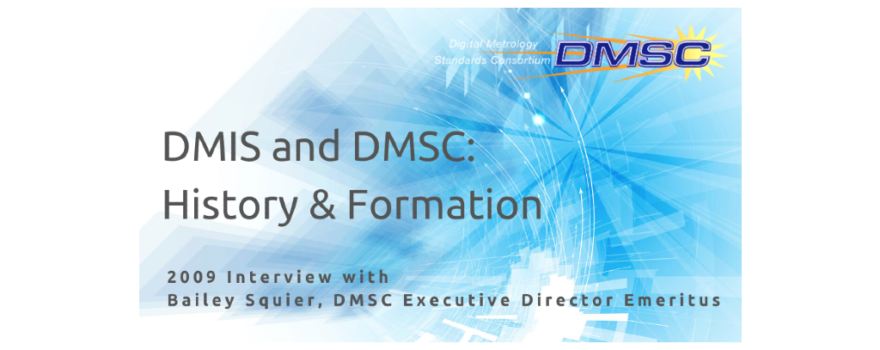
by Bailey Squier
DMSC Executive Director Emeritus
During our 2019 campaign to recruit and interview candidates to join the Digital Metrology Standards Consortium (DMSC) Board of Directors, questions arose about the history of the DMSC. It’s been nearly ten years since we first memorialized the evolution of the Dimensional Measurement Interface Standard (DMIS) and ultimately the formation of the Dimensional Metrology Standards Consortium (DMSC) in 2005.
While we’ve updated the name of the DMSC to Digital Metrology Standards Consortium, our mission, objectives remain constant. Many of the names associated with the creation of the DMIS standard are still with us today, bringing updated technology and strategies into the mix – including regular advancements to both standards in its care: DMIS and QIF.
Let’s dive into the first 25 years of DMSC history and give you the complete picture of where we’ve been
prior to the development of the QIF standard.
In 1983, an international consortium known at that time as Computer-Aided Manufacturing-International (CAM-I, Inc.) decided to initiate a Quality Assurance Interest Group for the purpose of investigating the benefits of research in the automation of Quality Assurance measurements and processes. CAM-I sent out a “call” to more than one hundred companies, users and suppliers, requesting representatives to attend this Interest Group meeting. The objective of the meeting was to decide if a CAM-I QA research program would be beneficial, and if so, what work should be undertaken. Approximately 80 representatives attended that first meeting in 1983, each with their own list of concerns and woes related to QA. The meeting was very productive as the group produced a list of more than 50 key issues that should be addressed within the Quality Industry. The issues were prioritized by vote, and narrowed down to 35 on the first pass. Several more rounds of redefining, discussions, and voting narrowed the list to the 10 top issues. The highest, most urgent issue on the list was the development of a “common communication language between automated inspection systems.” The intention from the very beginning was to make this language an official standard, a language that could be man-readable-and-writable, and could even be used as the internal language for the CMM Controller. Thus the CAM-I Quality Assurance Program (QAP) was born.
The need for a “common communication language” topped the list because at that time every CAD system produced its own output measurement language, and every coordinate measuring machine (CMM) had its own internal language that it would accept for processing. Thus, like the old APT machining program, translators and “post-processors” became rampant (a problem not quite yet solved). Every CAD system had to have a different output for every coordinate machine in the factory. A common language was desperately needed.
As an analogy, by International Treaty, every commercial airplane crossing any international border must speak the English language to the control tower where the plane is landing, and the control tower must speak the English language to the pilot of the airplane. The alternative would be that every pilot must learn to speak the language of every country that he might fly into, and every control tower operator must learn to speak the language of every country from which an airplane is likely to land at his airport. The situation was utter chaos until the international treaty was signed. Of course, several nations thought that their language would be more appropriate than English, but the fact is that more nations and more people speak English than any other language in the world.
Between 1983 and 1991, the QAP held many meetings to determine what this common communication language would look like, and what it would do. Some QAP chairmen included Bob Neshta, Richard Maragni of Grumman Aircraft; Don Schilling, AlliedSignal Aerospace; Sam Chapman, Lockheed Martin; Mike Kehoe, Kodak; Curtis Brown AlliedSignal Aerospace; and Jon Baldwin, Sandia National Laboratories. CAM-I’s QAP hired IITRI (the Illinois Institute of Technology Research Institute) to do the initial studies, the result of which identified many language formats that should not be used, and one that probably should. Later, Pratt and Whitney did further research, refining the work of IITRI, and producing the final language structure and format. The QAP member companies then went to work expanding and implementing the language until it became a useful tool for QA purposes. The language was named DMIS, for Dimensional Measuring Interface Specification. The QAP also coined the term, DME for Dimensional Measuring Equipment. DMIS versions 1.0 and 2.0 were prototypes, experimental in nature, and not quite ready to be progressed as a standard. When all the necessary funded research had been completed, a DMIS Technical Advisory Group (TAG) was created to continue maintenance and development. Finally, in 1991, DMIS version 2.1 was submitted to ANSI and accepted as an American National Standard.
Because of requirements from ANSI, the DMIS TAG transformed into the official DMIS National Standards Committee (DNSC). The DNSC became responsible for the development, maintenance, and sup-port of the standard, and was initially chaired by Richard Maragani. By 1995, Curtis Brown became the chairman and the DNSC produced DMIS version 3.0, which primarily added the thin-walled measurement enhancements into the standard, which was also approved by ANSI. Next, DMIS version 4.0 was completely restructured from version 3.0 in order to conform with ISO/IEC directives, Part 3. In addition to restructuring, DMIS 4.0 included a multitude of changes, like additional functionality in the areas of sensor definitions, sensor component grouping, complex alignment, CAD connectivity, soft functional gauging, quality information systems, relaxation of various length limitations, and operator interface using the PROMPT statement. The European DMIS Users Group (EDUG) was instrumental in developing, and supporting the development of many of these enhancements. DMIS 5.0 was developed by the DMIS National Standards Committee, still under the CAM-I umbrella, and became an ANSI standard on December 16, 2004.
As part of the development of DMIS 4.0, Gordon Hogg of Chrysler became the official Secretary of the DSC, and the “Document Custodian” for the DMIS Standard. His volunteer work to maintain the document; incorporate updates, fixes, new capabilities, any and all changes as voted in by the DMIS Standards Committee has made him indispensable as a major contributor to the success of the standard. In addition to being an expert in metrology, Mr. Hogg is the ultimate authority on the contents of the DMIS Standard. The excellence of his work as well as his dedication cannot be praised highly enough, especially since most was done on his own time.
Standards. As a result, the DMIS National Standards Committee had no home; i.e., no ANSI accredited sponsoring organization, and was essentially cast adrift. The DMIS Standard was in jeopardy. Based upon recommendations from conversations with legal counsel, the DNSC voted to incorporate as a separate legal entity, the Dimensional Metrology Standards Consortium (DMSC), and to hire Bailey H. Squier Associates (BHSA) to manage its day-to-day affairs. The DMSC was incorporated on June 13, 2005 in the state of Delaware as a not-for-profit organization. Its member companies constituting many of those who were members of the DMIS National Standards Committee, now known as the DMIS Standards Committee (DSC).
The mission of Dimensional Metrology Standards Consortium (DMSC, Inc.) is to identify needed standards in the field of dimensional metrology, and to promote, foster, and encourage the development of these standards, along with related and supporting standards that will benefit the industry as a whole. The DMSC is an ANSI accredited standards developing organization (SDO), as well as an A-Liaison with ISO/TC184/SC1. The Dimensional Measuring Interface Standard (DMIS) is only one standard that the consortium has the responsibility to develop, maintain and support as well as to coordinate and harmonize with other related standards efforts.
The information incompatibility problem in manufacturing metrology is costly to everyone: vendors, suppliers, end users, and customers. Standards are essential to national and world economies, and lack of interoperability between manufacturing automation systems wastes hundreds of millions of dollars every year. Recognizing the critical importance of industrial manufacturing and metrology standards, the Dimensional Metrology Standards Consortium (DMSC, Inc.) takes an active role in the establishment and coordination of these standards. Through member company representatives and participation, the DMSC is active in related national and international standards efforts.
Interoperability is a key factor in all DMSC activities. At the IMTS Expo in September, 2008, the DMSC demonstrated the value of using a standard programming language (DMIS) to allow different hardware and software producers to interface their products. The following diagram represents their interface connectivity and operation.
Unfortunately, many companies and organizations have taken it upon themselves to modify and change the DMIS Standard within their commercial implementations, to suit their own requirements and specifications. Since the integrity of the Standard must be maintained, and the chaos of multiple versions avoided; i.e., translators, post-processors, and incompatibilities, the DMSC has initiated the DMIS Certification Program. DMIS Certification is the testing of DMIS implementations for conformance to the standard. It is a means for OEMs to ensure that purchased products are in fact DMIS compliant and will be largely interoperable. It is also a way for suppliers to advertise and demonstrate DMIS conformance. To become certified means that that an applicant’s measurement software is syntactically 100% correct and 100% complete with the standard, in a particular DMIS conformance class. The DMSC defined the certification process, and Dr. Thomas Kramer of the National Institute of Standards and Technology (NIST) wrote the certification software.
DMIS Certification will enable interoperability; provide freedom of choice of software products; encourage competition; and reduce programming costs. End users using single vendor solutions can suffer if the vendor experiences economic issues, or becomes unstable because of a buy-out, and support can be weakened or eliminated by new management of previous systems. With standards, software providers can concentrate on providing viable solutions to end users, instead of translating existing software.
The DMSC invites participation within the consortium of other standards groups and activities that seek to resolve the technology and other issues of automated dimensional metrology. You can help by getting involved in these ways:
- joining the DMSC
- becoming active on DMSC working groups that help your industry
- including standardization requirements in your Purchase Orders and maintenance contracts to providers (e.g., DMIS, DML, eQuiPP).
BENEFITS OF DMSC MEMBERSHIP.
Three pages of DMSC member benefits are summarized here in a few words: Perhaps one of the greatest benefits of the DMSC is helping to increase company profits. Every manager, whether or not an MBA, knows that profits consist of money saved as well as money earned. The DMSC promotes the advancement of metrology technologies, their compatibility and interoperability, which result in cost savings. Several studies by independent organizations, as well as within industrial communities, report that lack of product compatibility costs industry hundreds of millions of dollars every year. Hundreds of millions of dollars, needlessly spent, divided among even a hundred companies, is more than a million-dollar a year savings each.
The DMSC also promotes the use of Dimensional Metrology (DM) as a viable tool for both manufacturing verification and product acceptance. In other words, the DMSC is marketing the purchase and use of more CMMs and other DM support hardware and software.
DMSC MEMBER COMPANIES – click here.
In closing, we would like to quote a well-known colleague from Ford Motor Company: “Who owns your company? You or your vendor?” That is, “With standards, you control your business… without standards, your vendors control it.”
Contact us if we can provide additional information, past or present, on DMIS and how you can get involved in the DMSC.
Note: Original article authored by Bailey Squier was published in CMM Quarterly in 2015.